压铸模具空蚀问题
摘要:压铸模具常见问题:空蚀(Cavitation)也称为气蚀。其较常见于运动的流体与气体之间相互作用在流体中形成负压力(拔空的孔洞)的气泡。当负压力的气泡在运动或流动的过程中遇到固体的表...
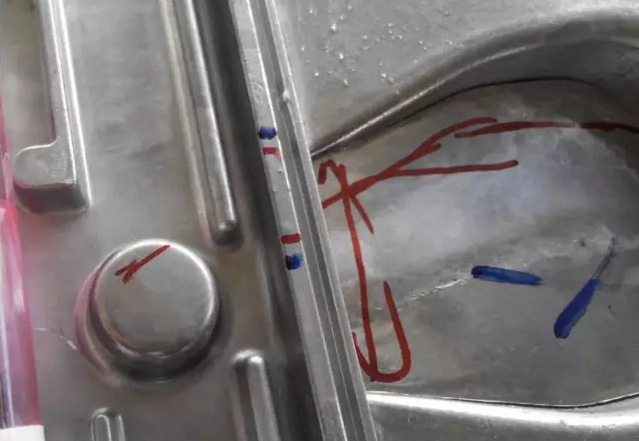
空蚀(Cavitation)也称为气蚀。其较常见于运动的流体与气体之间相互作用在流体中形成负压力(拔空的孔洞)的气泡。当负压力的气泡在运动或流动的过程中遇到固体的表面时,气泡湮灭释放巨大的爆破能量使得固体的表面形成凹孔。这种现象常见于在海水中使用的叶片,其表面由于水与旋动空气交互作用形成负压的气泡,其在叶片表面湮灭形成空蚀的凹坑,即通常讲的“麻点”。空蚀(Cavitation)也称为气蚀。 其较常见于运动的流体与气体之间相互作用在流体中形成负压力(拔空的孔洞)的气泡。当负压力的气泡在运动或流动的过程中遇到固体的表面时,气泡湮灭释放巨大的爆破能量使得固体的表面形成凹孔。这种现象常见于在海水中使用的叶片,其表面由于水与旋动空气交互作用形成负压的气泡,其在叶片表面湮灭形成空蚀的凹坑,即通常讲的“麻点”。
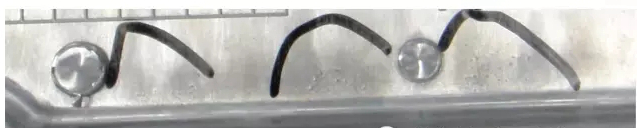
需要指出的是:在铝合金压铸件表面形成的“麻点”,除了”空蚀”原因外,还有其他原因会导致,如:模具表面放电加工后打磨不彻底、或模具表面过于光亮,使得脱模剂无法在模具表面形成良好的保护膜,导致在模具表面出现点状的溶蚀与粘模现象。但是“空蚀”在膜具表面产生的麻点与此类缺陷有形态上的不同,需要有足够的经验进行正确的判断。
铝合金压铸中空蚀产生的原因:
铝合金压铸是把液态的铝合金,由冲头高速推射到模具的整个型腔内,获得所需产品。铝液在流动过程中,需要经过浇道到达内浇口再喷射到模具型腔内。模具的浇道是铝液流动的必经路径。设计的原则是浇道的横截面积应当处于收缩状态, 这样铝液在流动过程中,可以将浇道内的空气排向铝液的前端。
空蚀产生的主要原因是模具设计时违背了以上的设计原则。在铝合金液体流动所经过的浇道路径上,浇道的横截面积有膨胀现象。当铝液经流膨胀的内浇道时会有体积的膨胀以及压力的突然下降,导致铝液中形成负压力(或拔空)的空穴。压射增压时, 空穴在浇道以及模具型腔内部破灭,。破灭时,形成内爆破,能够产生巨大的能量。生产产品时,持续的多次内爆破导致金属模具或浇道的表面产生疲劳变形,形成肉眼可见的凹坑。相应的在铸件产品表面形成凸出的麻点。如图所示。
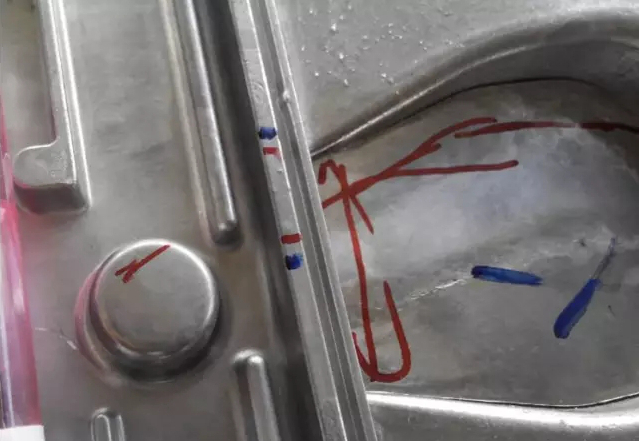
空蚀在膜具表面上的形态:
模具表面在生产了300件产品后,产生的局部空蚀的扫描电子显微镜照片。 可以看到:模具的表面被铝合金液体中的负压气泡在破灭时,由于反复的向内爆破使得金属模具表面形成疲劳变形。负压的气泡湮灭时所释放的能量破坏了模具的表面,在模具的表面形成爆破后的凹孔。 模具在持续生产后空蚀严重时,所导致的模具表面的严重损坏。
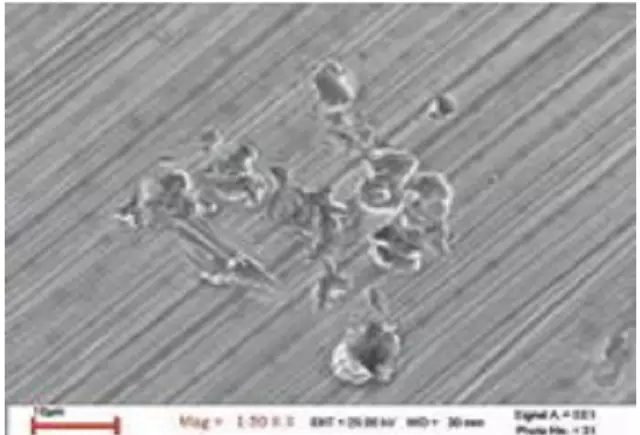
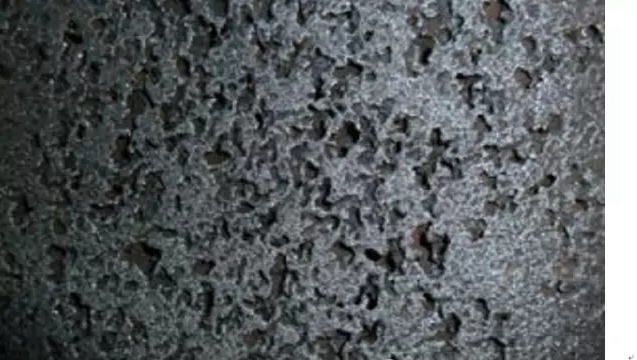
高压压铸中避免空蚀的方法——正确的模具浇道设计:
在模具浇道设计时需要遵守这样的原则:从料饼开始浇道的横截面积需要减小,并且当浇道有分支时主浇道的横截面积需要大于两个或者多个分支浇道横截面积的总合。具体举例:如图5.所示的浇道设计中,A的主浇道分成B-E 两个分浇道。A的横截面积是825平方毫米,B的横截面积是567平方毫米而E的横截面积是750平方毫米。此时两个分支浇道的横截面积的总合是1317平方毫米,而A作为主浇道的横截面积是850平方毫米。其结果是A<B+E,这样设计的模具在压铸时会产生空蚀现象。正确的浇道设计应当是A>B+E,这样才能避免空蚀的发生。
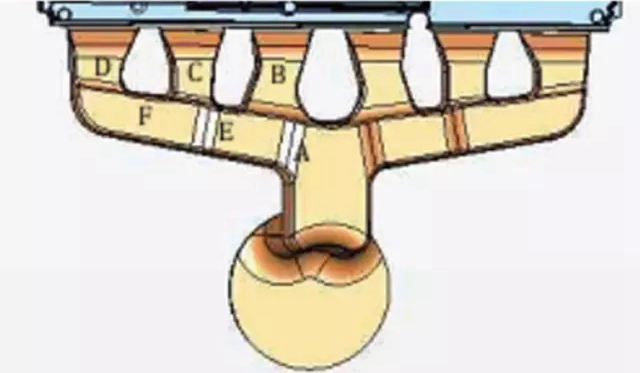
表面处理不能解决空蚀问题:
对模具材料采取表面处理是否能够解决空蚀在模具表面形成的“麻点”?
模具材料经过了PVD涂层处理后, 模具表面的侧视金相照片。可以看出,空蚀还是可以在模具表面形成“麻点”孔洞。铝合金中负压的气泡在压铸时多次破灭所释放的能量足以击穿高硬度的涂层,并且在模具表面形成孔洞。
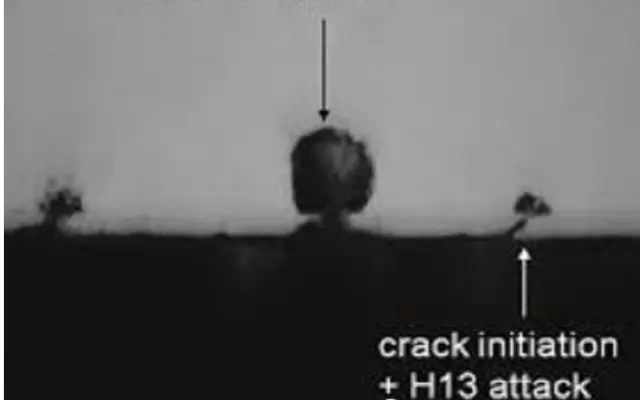
H13材料的压铸模具,压铸模具,通常使用的硬度是46-48HRC(≈470HV),而经PVD(TiCN)涂层处理后,其显微硬度是2200HV左右。 虽然提高了模具表面硬度, 但是对于解决空蚀问题依然无济于事。
总结:
空蚀在铝合金压铸过程中也是较为常见的质量问题。克服此类问题需要在模具的设计过程中,对整个浇道系统有良好的考量与计算,确保浇道从料饼到内浇口的整个流道处于压缩状态。采用表面处理提高模具的表面硬度的方法不能解决压铸的空蚀问题。