铝合金压铸裂纹分析及解决方案
摘要:铝合金压铸件的基体被破坏或断开,形成细长的缝隙,呈直线状或波浪形的纹路等不规则 形状,在外力作用下有发展的趋势,这种缺陷称为裂纹。裂纹产生的原因有很多种,如合金成分...
形状,在外力作用下有发展的趋势,这种缺陷称为裂纹。裂纹产生的原因有很多种,如合金成分,压铸模的模腔整体温度不合理;铝合金压铸件壁厚、薄处存有剧烈变化之处,收缩受阻,尖角位形成应力;工艺参数不合理等。铝合金压铸件中裂纹是不允许存在的。
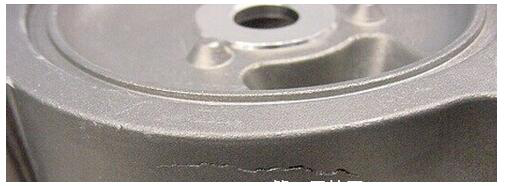
铝合金金铸件的裂纹产生原因:
1、中铁含量过高或硅含量过低
2、合金中有害杂质的含量过高,降低了合金的可塑性
3、铝硅合金,铝硅铜合金含锌或含铜量过高;铝镁合金中含镁量过多
4、模具,特别是型芯温度太低
5、铸件壁厚变化剧烈
6、留模时间过长
7、顶出时受力不均
压铸过程中存在的质量问题:
1.毛坯锻造质量问题,有些模具只生产了几百件就出现裂纹,而且裂纹发展很快。有可能是锻造时只保证了外型尺寸,而钢材中的树枝状晶体、夹杂碳化物、缩孔、气泡等疏松缺陷沿加工方法被延伸拉长,形成流线,这种流线对以后的最后的淬火变形、开裂、使用过程中的脆裂、失效倾向影响极大。
2.在车、铣、刨等终加工时产生的切削应力,这种应力可通过中间退火来消除。
3.淬火钢磨削时产生磨削应力,磨削时产生摩擦热,产生软化层、脱碳层,降低了热疲劳强度,容易导致热裂、早期裂纹。对h13钢在精磨后,可采取加热至510-570℃,以厚度每25mm保温一小时进行消除应力退火。
4.电火花加工产生应力。模具表面产生一层富集电极元素和电介质元素的白亮层,又硬又脆,这一层本身会有裂纹,有应力。电火花加工时应采用高的频率,使白亮层减到最小,必须进行抛光方法去除,并进行回火处理,回火在三级回火温度进行。
模具处理过程中:
热处理不当,会导致模具开裂而过早报废,特别是只采用调质,不进行淬火,再进行表面氮化工艺,在压铸几千模次后会出现表面龟裂和开裂。钢淬火时产生应力,是冷却过程中的热应力与相变时的组织应力叠加的结果,淬火应力是造成变形、开裂的原因,固必须进行回火来消除应力。
压铸生产过程中:
1. 模温
模具在生产前应预热到一定的温度,否则当高温金属液充型时产生激冷,导致模具内外层温度梯度增大,形成热应力,使模具表面龟裂,甚至开裂。
2. 充型
在生产过程中,模温不断升高,当模温过热时,容易产生粘模,运动部件失灵而导致模具表面损伤。 应设置冷却温控系统,保持模具工作温度在一定的范围内。
3. 开模
在抽芯、开模的过程中,当某些元件有形变时,也会产生机械应力。
4. 生产过程
在每一个压铸件生产过程中,由于模具与金属液之间的热交换,使模具表面产生周期性温度变化,引起周期性的热膨胀和收缩,产生周期性热应力。如浇注时模具表面因升温受到压应力,而开模顶出铸件后,模具表面因降温受到拉应力。当这种交变应力反复循环时,使模具内部积累的应力越来越大,当应力超过材料的疲劳极限时,模具表面产生裂纹。
预防模具损伤的措施:
1.良好的铸件结构设计
铸件壁厚尽可能均匀,避免产生热节,以减少模具局部热量集中产生的热疲劳。铸件的转角处应有适当的铸造圆角,以避免模具上有尖角位导致应力产生。
2.合理的模具结构设计
1)模具中各元件应有足够的刚度、强度,以承受压力而不变形。模具壁厚要足够,才能减少变形。
2)浇注系统设计尽量减少对型芯冲击、冲蚀。
3)正确选择各元件的公差配合和表面粗糙度。
4)保持模具热平衡
3. 规范热处理工艺
通过热处理可改变材料的金相组织,保证必要的强度、硬度、高温下尺寸稳定性、抗热疲劳性能和材料切削性能。
正确的热处理工艺,才会得到最佳的模具性能,而钢材的性能是受到淬火温度和时间、冷却速度和回火温度控制。
4. 压铸生产过程控制
1)温度控制:模具的预热温度和工作温度;合金浇注温度,在保证成型良好前提下,用较低的浇注温度。
2)合理的压铸工艺:比压、充填速度。
3)调整机器的锁模力,使模具受力均匀。注意清扫模具表面的残削碎片,以免合模时这些多余物使模具表面受力不均匀,引起变形。
4)对合金熔炼严格控制,减少金属液中气体。
改善措施:
正确控制合金成分,在某些情况下可在合金中加纯铝锭以降低合金中含镁量或铝合金中加铝硅中间合金以提高硅含量;改变铝合金压铸件结构,加大圆角,改变起模斜度,减少壁厚差;变更或增加顶出位置,使顶出受力均匀;缩短开模及抽芯时间;控制模温,保持模具热平衡。
压铸铝合金缸体水泵附近的水套底部裂纹现象:
铝合金缸体压铸生产后,通过检验,发现在水泵附近的水套底部有内外贯穿的裂纹,裂纹最长可达50mm,裂纹周围表面质量较差,如图所示。