铝合金压铸工艺参数分析与计算
摘要:为了便于分析压铸工艺参数,下面示出如图5-1和图5-2所示的卧式冷室压铸机压射过程图以及压射曲线图。 压射过程按三个阶段进行分析 第一阶段(图5-1b):由)0 -Ⅰ和Ⅰ-Ⅱ两段组成。 0...
压射过程按三个阶段进行分析
第一阶段(图5-1b):由)0 -Ⅰ和Ⅰ-Ⅱ两段组成。0 -Ⅰ段是压射冲头以低速运动,封住浇料口,推动金属液在压射室内平稳上升,使压射室内空气慢慢排出,并防止金属液从浇口溅出;Ⅰ-Ⅱ段是压射冲头以较快的速度运动,使金属液充满压射室前端并堆聚在内浇口前沿。第二阶段(图5-1c):Ⅱ-Ⅲ段,压射冲头快速运动阶段,使金属液充满整个型腔与浇注系统。
第三阶段(图5-1d):Ⅲ-Ⅳ段,压射冲头终压阶段,压射冲头运动基本停止,速度逐渐降为0。
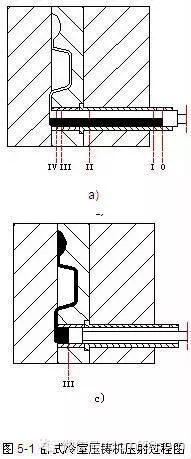
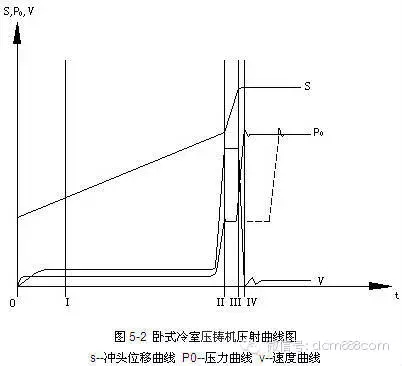
1、压力参数
(1)压射力 压射冲头在0-Ⅰ段,压射力是为了克服压射室与压射冲头和液压缸与活塞之间的摩擦阻力;Ⅰ-Ⅱ段,压射力上升,产生第一个压力峰,足以能达到突破内浇口阻力为止;Ⅱ-Ⅲ段,压射力继续上升,产生第二个压力峰;Ⅲ-Ⅳ段,压射力作用于正在凝固的金属液上,使之压实,此阶段有增压机构才能实现,此阶段压射力也叫增压压射力。(2)比压 比压可分为压射比压和增压比压。 在压射运动过程中0-Ⅲ段,压射室内金属液单位面积上所受的压射力称为压射比压;在Ⅲ-Ⅳ段,压射室内金属液单位面积上所受的增压压射力称为增压比压。比压是确保铸件质量的重要参数之一,推荐选用的增压比压如表5-1所示。
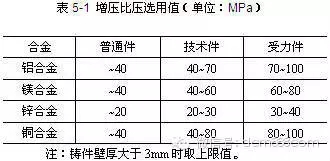
F主=APb/10
F主-主胀型力(KN); A-铸件在分型面上的投影面积(cm2); Pb-压射比压(MPa)。
分胀型力(F分)的大小是作用在斜销抽芯、斜滑块抽芯、液压抽芯锁紧面上的分力引起的胀型力之和。
(4)锁型(模)力 锁型(模)力是表示压铸机的大小的最基本参数,其作用是克服压铸填充时的胀型力。在压铸机生产中应保证型(模)具在胀型力的作用下不致胀开。压铸机的锁型(模)力必须大于胀型力才是可靠的,锁型(模)力和胀型力的关系如下: F锁 ≥K(F主 +F分) 式中 F锁--压铸机应有的锁型(模)力(KN); K--安全系数,一般取1.25; F主--主胀型力(KN); F分--分胀型力(KN)。 在压铸生产过程中,锁型(模)力大小的选择直接反映到压铸分型面处有否料液飞溅、铸件内组织的密度、有否气孔、成形是否完整、有否飞边及毛刺等。调整时,在保证铸件合格的前提下尽量减小锁模力。 为简化选用压铸机时各参数的计算,可根据压铸机具体的工作性能作出“比压、投影面积与胀型力关系图”,参见图5-3。在已知模具分型面上铸件总投影面积∑A和所选用的压射比压Pb后,能从图中直接查出胀型力。
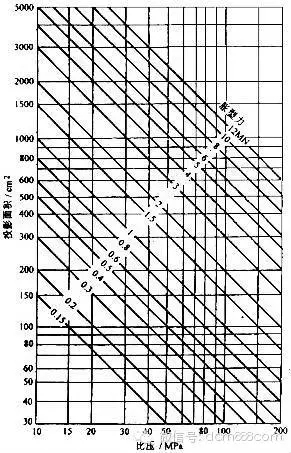
2、速度参数
速度的表示形式分为压射速度(即冲头速度)和填充速度(即内浇口速度)两种。压铸过程中的速度直接影响压铸件质量。一、速度参数 (1)低速速度 压射冲头将注入压室的铝液平稳地推移到内浇口位置,使铝液完全充满到压射冲头与内浇口之间的压室空间内的过程就是低速过程(一般为0.1-0.3m/s)。设置时要注意防止空气卷入,防止铝液温度下降,导致过早凝固。
(压室充满度的标准一般为20-50%) 例题:压室直径:Φ50mm,注入重量:830g,空打行程:368mm,压室截面积:(π/4)×52=19.63 cm2,溶液密度:2.6g/cm3 (2) 高速速度 压射冲头将铝液完全充满到压室内(一般为1.5-2.5m/s)。在铝液开始凝固之前,铝液的流动性好,压力的传递也好,所以填充时间越短,越容易得到质量好的铸件。 a. 填充时间 填充时间= 0.01X产品壁厚X产品壁厚 b. 依据模具条件的高速速度 c. 依据机器能力的高速速度 模具临界速度= (注:只考虑模具的浇口抵抗,充填抵抗时的实打速度) d. 确认浇口速度 (一般为40-60m/s) 例题:产品壁厚:3mm,产品+溢流重量:510g,压室截面积:19.63 cm2,浇口截面积:1.04cm2,铝液密度:2.6g/cm3 ,ACC压力:14MPa,压射缸截面积:(π/4)×112=95 cm2。 (3) 快慢速度转换行程 对于铝、镁合金来说,各个压射阶段的切换点尤为重要,比如低速在什么时候转入高速,高速什么时候转为增压等,直接影响到产品的表面和内部质量。 (一般考虑到行程开关的反应时间,转换行程可以延长1cm) 例题:产品+溢流重量:510g,压室截面积:19.63 cm2,空打行程:368mm,余料厚度:23mm,铝液密度:2.6g/cm3
(1)压射速度
压射室内冲头推动熔融金属液的移动速度,又称压射冲头速度,以m/s表示。在压射运动中,压射速度分为慢压射速度和快压射速度。
1)慢压射速度 压射冲头在压射运动的第一阶段(0-Ⅰ和Ⅰ-Ⅱ段)的移动速度。压射冲头将注入压室的铝液平稳地推移到内浇口位置,使铝液完全充满到压射冲头与内浇口之间的压室空间内的过程就是低速过程速度大小与压射室或冲头直径有关,压射室内径越大,速度值较低些;金属液充满度越高,速度值也低些。0-Ⅰ段一般选用0.1~0.3m/s,设置时要注意防止空气卷入,防止铝液温度下降,导致过早凝固;Ⅰ-Ⅱ段一般选用0.2~0.8 m/s 。
2)快压射速度 压射冲头在压射运动的第二阶段(Ⅱ-Ⅲ段)的移动速度。快速压射速度的大小直接影响金属液的填充速度,其速度大小与型腔容积、型腔数、冲头直径、填充时间有关。其计算公式如下
v压=4V/ π D2 t
v压--快速压射速度(m/s)
V --型腔容积(m3)
D --压射冲头直径(m)
t --填充时间(s)
(2)填充速度
金属液在压力作用下,通过内浇口进入型腔的线速度,又称为内浇口速度,由于型腔形状的多变性和复杂性,通常描述和设定的内浇口速度均指填充时段内的平均线速度。 过高的内浇口速度,会使铸件组织内部呈多孔性,力学性能明显降低,故对铸件内在质量、力学性能和致密性要求高时不宜选用高内浇口速度,而对于结构复杂并对表面质量要求高的薄壁铸件,可选用较高的冲头速度及内浇口速度。压射速度与填充速度的关系可以根据等流量连续流动原理(在同一时间内金属液以压射速度流过压射室的体积与以内浇口速度流过内浇口截面的体积相等)。即 A压V压=A内V充 V充= πD2 V压/ 4A内 式中 V充--填充速度(m/s) V压--压射速度(m/s) A压--压射室截面积(mm2) D --压射室内径(mm) A内--内浇口截面积(mm2) 要调整内浇口速度,可以通过调整压射冲头速度;改变压射室内径和冲头直径;改变内浇口截面积来直接改变内浇口速度。同时,快压射速度也可以通过浇口技术中的内浇口计算得出内浇口速度之后按公式求得。通常选用的内浇口速度范围如下:铝合金为30~60m/s; 镁合金为40~100m/s; 锌合金为25~50m/s;铜合金为25~50m/s。
(3)最大空压射速度
是指机器在空压射情况下的最大快压射速度。此项参数能反映压铸机的压射性能,见表5-2。
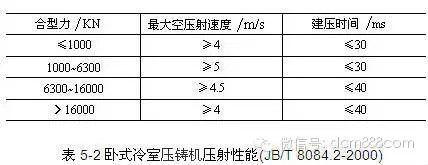
3、时间参数
(1)填充时间 金属液自内浇口开始进入型腔到充满压铸型(模)型腔的过程所需的时间,称为填充时间。填充时间应以"金属液尚未凝固而填充完毕"为前提。影响填充时间的因素为:金属液的过热度;浇注温度;压铸型(模)温度;排气效果;涂料隔热性与厚度等。填充时间的选用范围如表5-3所示。 表5-3 填充时间的选用范围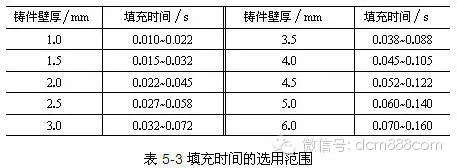
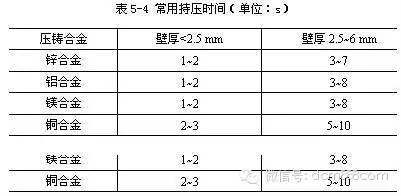
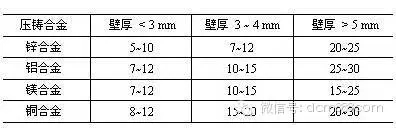
表5-5 常用留型(模)时间(单位:s)
4、温度参数
(1) 浇注温度 浇注温度一般指金属液浇入压射室至填充型腔时段内的平均温度,又称为熔融金属温度,通常在保证填充成形和达到质量要求的前提下,采用尽可能低的温度,一般以高于压铸合金液相线温度10~20℃为宜。各种压铸合金浇注温度的选择如下:铝合金为620~720℃; 镁合金为610~680℃; 锌合金为410~450℃; 铜合金为940~980℃。(2)压铸型(模)温度 压铸型(模)在生产前要预热,在压铸过程中要保持一定的温度。压铸型(模)总是处在热状态下工作的,这为合金液填充和凝固提供了基本保证。 各种压铸合金的压铸型(模)工作温度如下:铝合金为210~300℃;镁合金为240~300℃;锌合金为150~200℃;铜合金为320~420℃。 压铸型(模)预热可以避免金属液急冷,减少压铸型(模)的疲劳应力,压铸型(模)滑动部分的膨胀间隙,应在生产前预热时加以调整。 压铸型(模)加热方法有煤气加热、电加热器加热和远红外线加热几种。在加热时必须将推杆退回到压铸型(模)内,固定型芯与活动型芯的预热尽量达到使用温度,预热要均匀,预热后应进行清理和润滑。预热温度一般为150~180℃。
5、定量浇料和压射室充满度
(1)定量浇料压铸工艺参数中,热因素和冲头慢压射行程的计算与金属液浇入量有关,每一个浇入量必须精确或变化很小,通常称为定量浇注,所包括的重量和体积如下:
1)铸件净重(G1)和体积(V1)。
2)浇道系统内金属重量(G2)和体积(V2)。
3)压射室中余料(料饼)金属重量(G3)和体积(V3)。
4)排溢系统的金属重量(G4)和体积(V4)。
则浇入金属液总重量(G)和总体积(V)为:
G= G1 +G2+ G3+ G4
V= V1+ V2+ V3+ V4
(2)压射室充满度
压射室充满度即浇入压射室的金属量占压射室容量的百分数。充满度的大小直接影响铸件的含气率(气孔率)。 压射室充满度的计算如下
φ=(V/ V0)×100% 式中 φ-压射室充满度(100%),通常以40%~75%为宜;
V - 浇入金属液体积,(cm3或m3、mm3),V= G/ρ(G的单位为g或kg);
V0-压射室容积,包括压射室和型(模)具浇口套两部分的容积(cm3或m3、mm3),V0=(πd2/4)L ;
d-压射室内径(cm或m、mm);
L-压射室有效长度,包括型(模)具浇口套长度(cm或m、mm);
ρ-金属液的液态密度,铝合金 2.5g/ cm3(或2500kg/ m3、或0.0025g/ mm3),镁合金 1.7g/ cm3(或1700kg/ m3、或0.0017g/ mm3),锌合金 6.6g/ cm3(或6600kg/ m3、或0.0066g/ mm3),铜合金 8.0g/ cm3(或8000kg/ m3、或0.0080g/ mm3)。
铝合金压铸工艺参数计算
在压铸生产中,压铸机、压铸合金和压铸模是三大要素。压铸工艺则是将三大要素作为有机的组合并加以运用的过程。压铸生产时液态金属充型的过程,是许多矛盾着的因素得以统一的过程。在影响充型的许多因素中,主要是速度、压力和时间等,通过速度的控制减少和消除压室内空气的卷入、雾化型腔内残留的气体;通过压力的控制,增加产品的密实度,减少缩孔的形成;通过时间控制,使产品不宜产生变型等缺陷。利用计算工艺参数来优化模具、压铸机之间的匹配性。 因此,只有对这些工艺参数进行正确选择、控制和调整,使各种工艺参数满足压铸生产的需要,才能保证在其他条件良好的情况下,生产出合格的压铸件。本文通过某公司生产的280卧式冷室压铸机上所生产的水泵壳体产品(附图)为例,简单介绍一下压铸生产中主要工艺参数的计算(表一为相关参数)。
一、速度参数 (1)低速速度 压射冲头将注入压室的铝液平稳地推移到内浇口位置,使铝液完全充满到压射冲头与内浇口之间的压室空间内的过程就是低速过程(一般为0.1-0.3m/s)。设置时要注意防止空气卷入,防止铝液温度下降,导致过早凝固。 (压室充满度的标准一般为20-50%) 例题:压室直径:Φ50mm,注入重量:830g,空打行程:368mm,压室截面积:(π/4)×52=19.63 cm2,溶液密度:2.6g/cm3 (2) 高速速度 压射冲头将铝液完全充满到压室内(一般为1.5-2.5m/s)。在铝液开始凝固之前,铝液的流动性好,压力的传递也好,所以填充时间越短,越容易得到质量好的铸件。 a. 填充时间 填充时间= 0.01X产品壁厚X产品壁厚 b. 依据模具条件的高速速度 c. 依据机器能力的高速速度 模具临界速度= (注:只考虑模具的浇口抵抗,充填抵抗时的实打速度) d. 确认浇口速度 (一般为40-60m/s) 例题:产品壁厚:3mm,产品+溢流重量:510g,压室截面积:19.63 cm2,浇口截面积:1.04cm2,铝液密度:2.6g/cm3 ,ACC压力:14MPa,压射缸截面积:(π/4)×112=95 cm2。 (3) 快慢速度转换行程 对于铝、镁合金来说,各个压射阶段的切换点尤为重要,比如低速在什么时候转入高速,高速什么时候转为增压等,直接影响到产品的表面和内部质量。 (一般考虑到行程开关的反应时间,转换行程可以延长1cm) 例题:产品+溢流重量:510g,压室截面积:19.63 cm2,空打行程:368mm,余料厚度:23mm,铝液密度:2.6g/cm3
二、压力参数 (1)铸造压力 铸造压力是获得铸件组织致密和轮廓的主要因素,又是压铸区别于其他铸造方法的主要特征.其大小取决于压铸机的结构及功率。 (0.9为ACC压力下降) (2)涨型力 压铸过程中,充填型腔的金属液将压射活塞的比压传递至型(模)具型腔壁面上的力。 (3)模具临界压力 例题:增压缸截面积:(π/4)×162=201.1 cm2,ACC压力:14MPa,压室截面积:19.63 cm2 投影面积:204 cm2
三、时间参数 (1)填充时间 金属液在压力的作用下从内浇口进入型腔直到充满,这个过程所需时间。合金浇注温度高时,模具温高时,铸件壁厚部分离内浇口远时,熔化潜热和比热高的合金,填充时间可选择长一些。 (2)留模时间 从持压终了至开模这段时间,根据铸件厚薄、复杂结构选择。综合压铸过程的压铸工艺参数压力、速度、温度、时间选项择为:铸件壁厚、结构复杂,压力要大,留模时间要长;铸件壁薄、结构复杂,压射速度要快,模具温度要高; (3)增压时间 压铸件进一步得到致密的最终压力所使用的时间,增压压力的时间要比内浇口凝固的时间短,否则内浇口凝固,压力无法传递到铸件上。 (4)内浇口凝固时间 内浇口凝固的时间关系到压力是否能够传递到铸件上,铸件的内部质量是否能达到合格状态。 例题:产品壁厚:3mm,
四、生产实践 利用计算的结果我们对机床参数进行设定,通过试生产查看产品外观及内部质量,对参数进行了微调(具体参数见表二),再生产就可以生产出合格的产品出来,内部废品率只有不到1%。利用现有工艺参数,已经生产了五万多件,机加合格率在97%以上。有效的降低了频繁试模,调整参数的麻烦,优化了模具机床的匹配性。
五、结论 压铸生产中机器工艺参数的设定和调节直接影响产品的质量。一个参数可能造成产品的多个缺陷,而同一产品的同一缺陷有可能与多个参数有关,要求设计模具时要认真计算工艺参数并且在试压铸生产中要仔细分析工艺参数的变化对铸件成形的影响,压铸生产厂家通常要由专人设定和调节机床参数。