压铸模具设计对模具寿命的影响
摘要:压铸模具设计是影响压铸模具寿命一个重要因素,在压铸模具设计时必须根据铸件的特性,充分考量影响模具寿命的因素,合理地设计模具结构...
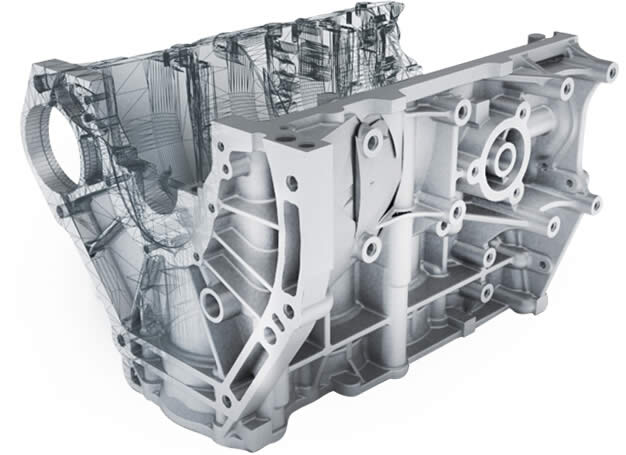
1、模具强度是否足够
模具强度是否足够是影响模具寿命的重要因素,对于这一点中国目前大部分企业,包括压铸企业在采购模具时,普遍特别关注模具价格,甚至认为,只要能压铸出合格产品就行,对于模具大小,模具强度是否足够没有引起足够重视。同时,很多压铸模具制造企业为了取得订单,往往把模具价格压低,而在模具制作时能省则省,以降低成本。模具强度如果不够不仅影响模具可靠性,也影响模具寿命。实际上从压铸生产的角度来看,这样的模具并不经济。压铸模具如果强度不够,刚性差,模具在不断的受冲击、受压的情况下,就会过早的开裂。并且由于封铝面太少,会造成模具窜铝,不及时清理又压踏模具,造成模具损坏。因此,在模具设计时必须充分考虑模具强度,确保模具寿命。
a 硬度硬度是模具钢的主要技术指标,模具在高应力的作用下欲保持其形状尺寸不变,必须具有足够高的硬度。冷作模具钢在室温条件下一般硬度保持在HRC60左右,热作模具钢根据其工作条件,一般要求保持在HRC40~55范围。对于同一钢种而言,在一定的硬度值范围内,硬度与变形抗力成正比;但具有同一硬度值而成分及组织不同的钢种之间,其塑性变形抗力可能有明显的差别。
b 红硬性在高温状态下工作的热作模具,要求保持其组织和性能的稳定,从而保持足够高的硬度,这种性能称为红硬性。碳素工具钢、低合金工具钢通常能在180~250℃的温度范围内保持这种性能,铬钼热作模具钢一般在550~600℃的温度范围内保持这种性能。 钢的红硬性主要取决于钢的化学成分和热处理工艺。
c 抗压屈服强度和抗压弯曲强度模具在使用过程中经常受到强度较高的压力和弯曲的作用,因此要求模具材料应具有一定的抗压强度和抗弯强度。在很多情况下,进行抗压试验和抗弯试验的条件接近于模具的实际工作条件(例如,所测得的模具钢的抗压屈服强度与冲头工作时所表现出来的变形抗力较为吻合)。 抗弯试验的另一个优点是应变量的绝对值大,能较灵敏地反映出不同钢种之间以及在不同热处理和组织状态下变形抗力的差别。
2、模具内浇口速度是否合适,应尽量偏低
压铸模具内浇口的设计既是影响铸件质量的重要因素,同时又直接影响压铸模具寿命,因此在压铸模具设计时必须高度重视。压铸模具内浇口速度越快,对模具型腔的冲击越大,模具型腔的瞬间升温越大,模具越容易出现表面龟裂或开裂。压铸模具内浇口一般在30-70米/秒为宜,并且在确保产品质量的情况下,尽量偏低,这样,可以降低对模具的冲击,从而延长模具寿命。在一定的压射条件下,内浇口面积过大时,会使填充速度过低,金属过早凝固,甚至导致充填不足;而过小的内浇口面积,会使喷射加剧,增加热量损失,产生涡流并卷入过多的气体,对模具冲刷加剧,导致模具早期报废。
a. 内浇口截面积的大小,常常是凭经验在设计绘图过程中来确定的,单纯地依据经验公式所计算内浇口的截面积,割裂了内浇口截面积与充填速度和充填时间的密切联系,内浇口截面积与充填速度和充填时间之间存在着不能有效匹配的风险,设计结果能在多大的工艺范围内进行修改,设计者并不清楚。
b. 内浇口截面积相差悬殊,生产实践中模具内浇口截面积与压铸件不匹配的情况屡见不鲜,当这种不匹配性差距不大时,其表现并不是很明显,在模具使用中,操作人员常常会感到模具不好用;当其差距较大时就会明显的表现出来,压铸件无法成形、废品率高、质量不稳定。
c. 生产过程中就会对工艺参数要求很高,工艺的略微波动会造成压铸件表面产生各种各样的缺陷,这样的模具如果放到一台性能更高的压铸机上生产也有可能顺利的生产合格的压铸件,但在现有的压铸机上是很难正常生产的。
3、模具滑块锁紧块强度是否足够
由于压铸是高速、高压,压铸模具滑块受的冲击力非常大,压铸比压一般选择在400-900公斤/平方厘米,以滑块投影100×100mm,为例,作用力就有40吨-90吨之大,因此,目前很多压铸模具企业在设计模具时普遍为了节省材料,模具设计偏小,锁紧块不够大,强度不够,从而造成滑块锁不住。不但会影响铸件质量,同时,容易造成窜铝,造成滑块卡死,造成模具锁紧部分变形或开裂,从而损坏模具,影响模具寿命。因此在设计模具时必须确保模具滑块锁紧块强度足够,确保模具的可靠性,延长模具寿命。
4、模具型腔封铝面是否足够
由于压铸是高温、高速、高压,压铸模具窜铝是时有发生的,究其原因,除了压铸参数选择不当,压射速度过快,压力太大,锁模力不够等以外,模具设计不合理,封铝面不够也是其中重要的原因。如果模具窜铝,一方面直接影响铸件的内部质量,另一方面,由于在压铸过程中,没有及时或难以清理,这样会把模具挤坏,造成模具分型面塌陷。更严重的在有滑块结构的模具中,如果窜铝窜到滑块间隙里,在合模时由于锁模力非常大,会把滑块或滑块座挤坏,甚至挤裂模架。这样的现象在压铸企业里经常发生。究其原因,主要是压铸企业或模具制造企业为了节省费用,把模具做的过小,封铝面不够大而造成的。有一个现象,值得我们反思,日本人是很节约的,但是,日本人做的压铸模具基本上比中国大部分厂家做的模具大,为什么?因为压铸模具如果仅仅考虑成本,而忽略了模具最关键的特性,即:可靠性、成品率、生产效率、寿命,将是得不偿失。这也是中国压铸模具与国外先进国家模具的差距所在。这个观念不仅仅是压铸模具制造企业需要改变,同样也是压铸模具使用企业应该扭转的。 因此,在设计模具时应高度关注封铝面特别是在滑块部位的封铝面,必须足够,以确保不窜铝,从而延长模具寿命。
5、模具冷却(加温)设计是否合理,模具温度场是否合理
模具冷却水设计在压铸模具的设计中是至关重要环节,在中国大部分压铸模具制造厂家,往往对于浇注系统非常重视。
模具的温度会过高甚至达到无法正常生产的底部;模具也有可能由于温度过高造成模具变形超标而报废;更会造成模具寿命大幅度降低;还有就是会造成模具表面高温氧化失效。
很多厂家在使用模流分析软件时,往往对于填充部分研究得很多,而对于模具温度场变化研究的不多。实际上在压铸生产中,模具冷却、模具温度场变化,对于生产效率、铸件质量以及模具寿命都是至关重要的。有条件可以使用压铸专用模温机,有助于提高生产效率,提高铸件质量,同时也可以延长模具寿命。 铝合金压铸模具在使用过程中,由于液态铝合金在瞬间填充模具型腔使得模具表面承受高温而表面温度升高。压铸铝合金产品的冷却成形是模具材料做为导热体把铝合金凝固过程散发的热量传递到模具内部。由于压铸成形的产品形状不规则,即产品的厚度不均匀,那么铸件产品在凝固过程中所散发的热量是不同的。模具设计过程中,需要有效的设计模具的内冷却水道分布使得模具表面温度差降低到最小。这样才能减少模具表面温度差异从而控制压铸产品的变形,减少缩孔的发生,保证班产量与生产节拍。 模具温度场的控制需要在模具设计的初期就考虑周全。也就是说,需要设定好班产量与生产节拍(如:60件产品/小时)从而了解模具在生产过程中所散发的热功率。在了解模具不同厚薄部分在生产时所散发的热功率后,计算出冷却水道的直径,距离表面的距离,以及冷却水的流量,从而控制模具表面温度在240度。 目前常见的问题是,温度场的建立不是在计算的基础之上,而且根据经验大致估计一下冷却水道距离表面的距离,以及冷却水道的孔径。其结果是,模具表面温度难达到均匀。当模具局部有过热时,采用大量喷涂脱模剂的方法来冷却模具。这样的结果是,模具在使用很短一段时间后,如3000多模次,模具表面出现热疲劳裂纹。在其后的生产过程中,由于模具持续承受剧烈的冷/热循环导致模具早期失效达不到预定的8-10万模次寿命要求。从而大大的减少的模具的寿命。因此,优化模具冷却(加温)设计是提高模具成品率、生产效率的关键,同时也是延长模具寿命的非常重要途径。
6、易损部位是否镶拼
为了延长模具寿命,在模具设计时,复杂的型腔可以进行分块加工简化工艺,对于易出现模具开裂、模具损坏的部位进行镶拼,一方面便于维修和更换降低模具制造成本;另一方面,镶拼接缝可以阻隔开裂的延展。也避免了局部开裂延展到其他部位,从而延长模具寿命。
7、减少应力集中的尖角
尖角处容易应力集中,因此,对于压铸件,转角处的尖角,无论从铸件的浇注过程,还是铸件质量,以及压铸模具寿命都是影响非常大的。因此,在前期与铸件设计人员探讨问题时,应非常关注铸件的转角,能大的尽量加大,这一点非常重要。
8、采用先进的技术
为了延长模具寿命,包括中国在内的很多科技人员都在积极探索一些新的技术,如表面新的渗氮技术、镀钛,表面微细网格延寿技术等等。因此作为压铸模具的制造企业,作为压铸模具设计人员,积极探索新的技术,及时跟踪先进技术,适时采用新的技术提高模具寿命,也是提升压铸模具水平、提升企业技术水平的有效途径。辉旺公司在这方面进行了探索,应用了很多新的技术,取得了很好的效果。