模流分析对应压铸缺陷分析优化
摘要:通过模流分析结果指导产品设计、模具设计和压铸生产,浇口位置、流道浇口大小、水道等优化模具设计图来满足实际试模成型要求,改进模具设计方案,降低模具成本减少试模次数,对...
模流分析结果用的好可以有效避免模具设计和成型风险,有效减少模具反复修改成本,有效降低模具试模调机次数。是模具压铸生产很有效的前期风险分析手段。
博威模具在压铸生产前做以下数据分析。
•Product data analysis 产品数据分析
我们根据客户产品分析 产品的基本数据,包括:结构、厚度、数据质量等
•Gate Location 浇口位置
根据客户产品要求,为客户分析选择最佳的进浇口方式、流道大小、浇口大小,满足客户要求并使产品达到最佳充填状态,我们有丰富的经验。
•Cool system 冷却系统
为客户建议效果最优的模具冷却系统,既能保证产品质量又能缩短冷却时间。
•Fill time 充填时间
根据产品结构和材料提醒为客户设计最优的产品充填时间要求,包括保压切换时间等。
•Flow Front Temp
流动前沿温度 根据塑胶流动特点准确分析产品和模具温度。
•Pressure at V/P switchover 最大注射压力
为客户提供最佳成型参数。
•Clamp Force 锁模力
为客户提供最佳成型参数,为机台选择和调机提供数据参考。
•Cycle time 周期预测
经过分析为客户提供合理的成型周期预测,为客户的试模调机、注塑生产和产能预测提供可靠的数据支撑。
•Sink mark 缩痕
•Air Traps 困气
•Weld Lines 结合线
通过分析,提前预测产品缺陷部位,提前预防成型风险。
•Volumetric shrinkage 体积收缩
通过精确分析,为模具设计提供收缩率数据参考。
•Deflection (total, X, Y, Z direction) 变形
通过模流分析可以准确分析产品各个方向的变形,做到前期风险预测。
•Suggestions 分析
我们根据综合分析结果为产品设计、模具设计和成型调机提供重要依据,对压铸模具做出最优改善方案。
一套模具反复试模,改了这几个问题,又出现了其他问题,改浇口位置、改流道浇口大小、通过修改产品来满足成型要求,反复试模非常浪费成本。根本问题是模流分析(CAE)和产品前期评估(DFM)能力问题。模具是个比较传统的行业,沉淀下了很多经验丰富的老一辈模具技术和管理人员,模具厂老板往往也是技术出身,经验丰富。要么靠经验判断,要么技术人员没有经过专业培训,仅仅能够使用分析软件进行简单分析,对压铸成型原理、模具结构、问题分析能力欠缺,造成分析结果不准确,分析结果同实际试模生产差距较大,不能指导产品设计、模具设计和压生产没有用到模流分析的好处。模流分析未卜先知之术,我们通过模具生产最常见的几个问题来了解模流分析及模具改进优化方案。
一 流痕
1.1原因分析
材料在浇口附近冻结。低熔体或模具温度,以及低螺杆速度会导致冷料进入型腔。这会导致未完全固化的材料呈现出流动模式的形态。
1.2流痕现象在的模流分析平均速度结果和流动结果中检查。
1.3流痕案例分析介绍
二 迟滞
2.1原因分析
进入型腔的熔体填充较薄部位和较厚部位时,它会先填充较厚部位,因为较厚部位的路径对流动产生的阻力小。这会导致熔体在较薄部位中的流动停止或明显减速。迟滞会降低零件质量,体现为表面外观发生变化、保压差、应力高和塑料分子的取向不均。如果迟滞使得流动前沿完全冻结,那么部分型腔可能保持未填充状态,从而导致短射。 熔体一旦开始减速,便会快速冷却,粘度也会因此加大。高粘度转而又会进一步抑制流动,导致冷却速度更快,因而此问题可自我扩展。迟滞会在加强筋中和壁厚变化明显的零件的较薄部位产生。在下图中,加强筋以红圈圈出。由于此处比零件的其余部分薄得多,因此对于流动的阻力较大。
采取以下步骤也可减少迟滞:
移动聚合物注射位置,使其远离迟滞区域,这样便会在熔体到达薄区域之前先填充型腔的主体。没有其他的可选流动路径,留给聚合物迟滞的时间就会减少。
将聚合物注射位置移至将因此而使用较大压力的迟滞发生处。将薄加强筋/定位柱作为最后的填充点是很有用的,这样便可使所有的注射压力均施加于此点。
增大迟滞发生处的壁厚可减少流动阻力。
使用粘性较小的材料(即,熔体流动指数较高的材料)。
加快注射速度可减少潜在的迟滞时间。
提高熔体温度,以使熔体更容易地流入薄区域。

2.2:迟滞现象在模流分析流动结果中检查。
如下图所示黄色区域等高线密集,产品存在严重的迟滞。
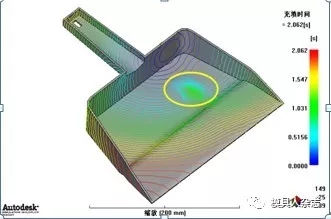
2.3:迟滞案例分析介绍
三 缩痕
3.1:缩痕原因分析
缩痕在成型零件的表面显示为凹陷。这些凹陷通常非常小;不过,它们通常看起来很明显,因为其会朝零件的不同方向反光。缩痕的可见性是零件的颜色和表面纹理的共同作用的结果,因此深度仅仅是其中的一个标准。尽管缩痕并不影响零件强度或功能,但还是将其视为严重的质量缺陷。 缩痕主要由冷却期间的热收缩造成。外部材料冷却并固化后,型芯材料才开始冷却。型芯材料的收缩将主壁表面拉向内侧,产生缩痕。如果表层足够刚硬,则表层的变形就会被型芯中缩孔的形成所取代。常见的发生缩痕有以下几种情况:
· 局部几何特征。缩痕通常出现在包含较厚部位的成型物中,或者出现在与加强筋、定位柱或内圆角相对的位置。
· 体积收缩率高。 · 材料补偿不足。浇口冻结过早或保压压力过低可能会使型腔无法正常保压。
· 保压或冷却时间短。
· 熔体和/或模具温度高。
如果零件的外表层足够坚硬,便可以抵抗收缩力从而避免表面凹陷。相反,材料型芯会收缩,在零件内部产生缩孔。如下图。
3.2:缩痕现象在模流分析软件的体积收缩结果和缩痕深度结果中检查。
3.3:缩痕案例分析介绍。
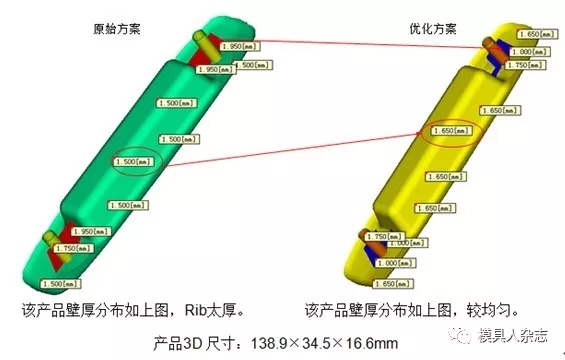

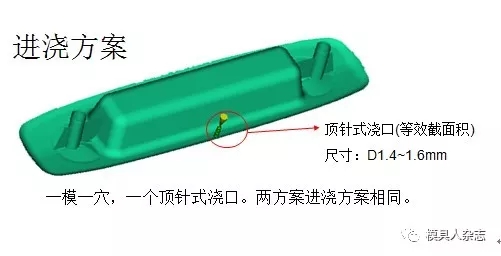
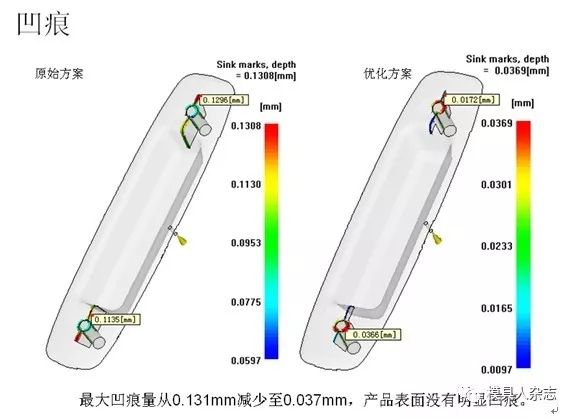
通过优化产品和Rib壁厚,并降低模温和料温,加大保压压力后,产品凹痕量从0.131mm减少至0.037mm,产品表面没有明显的凹痕